https://www.templa-kunststofftechnik.com/
Mit dem Mut zur Veränderung und der Entschlossenheit, Widerstände zu überwinden, hat das aufstrebende Produktionsunternehmen Templa Kunststofftechnik seine Fertigung digital vernetzt und sich strategisch neu aufgestellt. Zentrale Impulse: energiesparende elektrische Maschinen, proaktives Energiemanagement, Instrumente für mehr Nachhaltigkeit und Effizienz. Und die Bereitschaft, auf den eigenen gesunden Menschenverstand zu vertrauen.
Das 2017 gegründete Unternehmen aus dem mittelfränkischen Veitsaurach ist als Zulieferer für eine große Spielzeugmarke erfolgreich. Dann kam Corona, brachte die Auftragslage durcheinander und führte dazu, dass sich das Unternehmen – wie so viele andere in der Pandemie – zum Lohnfertiger entwickelte. Statt den Kopf in den Sand zu stecken, hat das Team um Geschäftsführer Peter Müller bewiesen, dass auch ein mittelständisches Unternehmen mit einem hohen Maß an Flexibilität, Ideenreichtum und dem Mut zur Weiterentwicklung viel erreichen kann.
Heute deckt die Templa Kunststofftechnik GmbH & Co. KG ein breites Spektrum an Kompetenzen ab, von der Produktentwicklung bis zur nachgelagerten Montage und Verpackung der produzierten Teile.
Der Maschinenpark umfasst unter anderem 22 Kunststoff-Spritzgießmaschinen mit Schließkräften von 30 bis 230 Tonnen und Schussgewichten von 0,1 bis 500 Gramm, darunter sechs elektrische Maschinen vom Typ Zhafir Zeres mit Schließkräften von 90 bis 230 Tonnen.
Es wird eine breite Palette von Materialien verarbeitet, wie z.B. Thermoplaste mit hohem Füllstoffgehalt (Glasfasern/Kugeln, Talkum), thermisch empfindliche Kunststoffe oder Hochtemperaturkunststoffe (PPS, PPO, PEEK, etc.).
Insgesamt stellt Templa mit nur 12 Mitarbeitern auf einer Produktionsfläche von rund 1.000 Quadratmetern etwa 65 Millionen Kunststoffteile pro Jahr her, darunter auch Hybridteile wie Einsätze, Buchsen, Kerne usw. Schnell wird klar, dass das Team auf eine schlanke, prozesssichere Produktion in der Kunststoffverarbeitung setzt, bis hin zur direkten Verpackung der produzierten Teile in die Lieferverpackung. Die gesamte Peripherie der Spritzgießmaschinen ist digital vernetzt, die Null-Fehler-Produktion ist längst Standard.
„Themen wie Unternehmen 4.0, Industrie 4.0 oder Produktionsstrategie 4.0 sind für uns kein Jargon oder Trendbegriffe“, sagt Peter Müller. „Sie sind Teil unserer täglichen Arbeit und die Basis des Unternehmenserfolgs. Mit unseren voll vernetzten, automatisierten und optimierten Prozessen können wir extrem kurze Durchlaufzeiten beim Spritzgießen realisieren und schnell und flexibel agieren, was zu einem sehr guten Preis-Leistungs-Verhältnis führt.“
Der Energieverbrauch jeder einzelnen Maschine wird mit dem Energiemanagement-Tool Sensorfact überwacht und optimiert. So lässt sich der Stromverbrauch jeder einzelnen Maschine leicht ermitteln und die Gesamteffizienz des Betriebs verbessern. Es hat sich herausgestellt, dass die Zhafir-Maschinen hervorragende Verbrauchswerte in Bezug auf Energie haben, was sie von nun an zur „ersten Wahl“ bei der Produktionsplanung macht. Das macht uns neugierig, wir wollen es genau wissen und bitten Peter Müller um einen konkreten Vergleich von Verbrauchsdaten.
Im Vergleich zeigt die elektrische Maschine klare Vorteile
Die Einstellung ist schnell definiert: Im 28-Sekunden-Takt soll ein technisches Teil aus PP TV20 hergestellt werden, mit einem Schussgewicht von ca. 90 g und einem hohen Anspruch an Maßhaltigkeit und Qualität. Im Wettbewerb stehen eine hydraulische Maschine eines bekannten Herstellers mit 80 Tonnen (grüne Linie) und eine Zhafir Zeres mit 120 Tonnen (blaue Linie), beide ausgestattet mit hydraulischem Kernzug und 6-facher Heißkanalregelung. Beide Maschinen laufen mit einem Temperiergerät, das etwa 1,5 KW verbraucht, was ebenfalls gemessen wird.
Das Ergebnis ist mehr als deutlich: Der Zeres arbeitet um gut ein Drittel energieeffizienter.
Die Screenshots des Powermanagements machen es deutlich: Der Stromverbrauch des Zeres (blau) liegt rund 30% unter dem der hydraulischen Markenmaschine, was den klaren Vorteil der energiesparenden Technologie von Haitian International unterstreicht.
Peter Müller wusste es von Anfang an: „Wenn es darum geht, Strom zu sparen, schalten wir zuerst die Zeres ein, das spart uns richtig Geld.“
Auf die Frage nach seinen Erwartungen für die künftige Markt- und Kostenentwicklung lächelt Peter Müller entspannt und sieht sein Unternehmen bereits recht gut aufgestellt. „Wir sind bei dem Projekt sehr effizient und haben eine kurze Markteinführungszeit. Wir verfügen über ein hohes Maß an technischem Know-how in der Fertigung, produzieren auf energieeffizienten Maschinen und unser CO2-Fußabdruck ist bereits ziemlich klein.“
Müller vertraut auf den eingeschlagenen Weg und setzt weiterhin auf Offenheit für Neues und innovative Lösungen. Dies hat sich langfristig ausgezahlt, sagt er und nennt einige Beispiele:
- Mit einem 3D-Scanner von GOM Metrology (Teil der ZEISS Gruppe) konnten Templa und seine Werkzeuglieferanten ihre Prozessdurchlaufzeiten „erheblich reduzieren“. Die vollflächige Geometrieerfassung durch 3D-Scannen bilde die Datengrundlage für die Prüfung von Formen und Kunststoffteilen in der Qualitätskontrolle, sagte er.
- Die durchschnittliche Korrekturschleife von Spritzgießwerkzeugen konnte durch den Einsatz der Simulationssoftware CADMOULD und Varimos um satte 50% auf durchschnittlich 1,25 Schleifen pro Werkzeug reduziert werden. „Eine erhebliche Zeit- und Kostenersparnis für unsere Kunden“, so Müller.
- Außerdem, so sagt er, werden jetzt norddeutsche Cleantower-Systeme zur optimierten Wartung der Maschinen und Werkzeuge eingesetzt. Kriechende Rost- und Kalkablagerungen in den Kühlkanälen „gehören damit der Vergangenheit an“ und man hat „immer die volle Kühlleistung und damit eine konstante Teilequalität“.
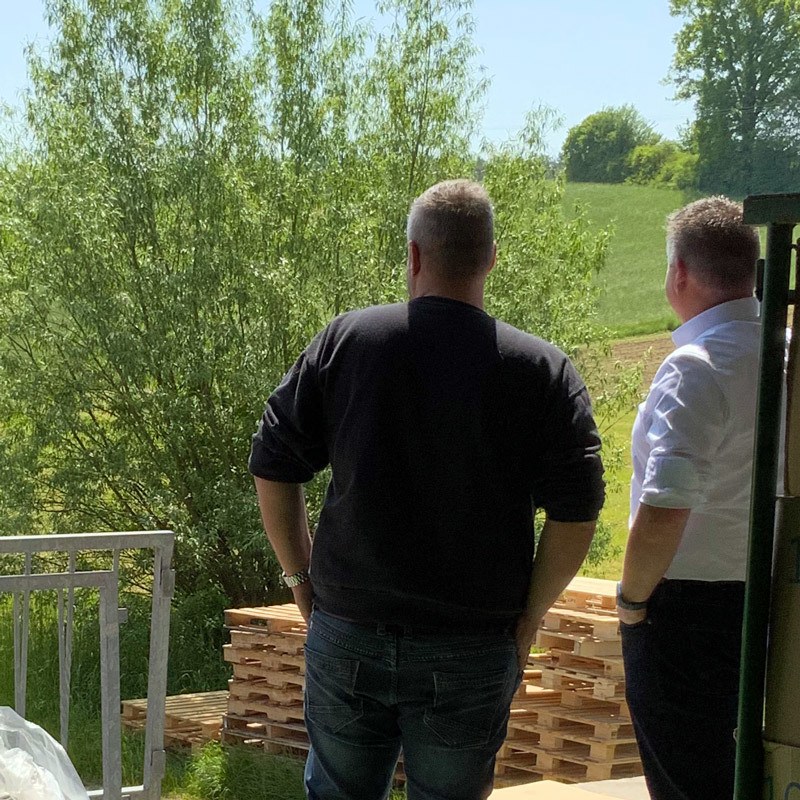
Peter Müller, Geschäftsführer von Templa (links) und Christian Färber, Vertriebspartner von Haitian International Deutschland, werfen einen Blick in die Zukunft.
Ein Hidden Champion mit einer klaren Mission
Der Erfolg von Templa zeigt, dass auch kleine Unternehmen bemerkenswerte Ergebnisse erzielen können, wenn sie fortschrittliche Technologien einsetzen und dabei auf Nachhaltigkeit achten. Wenn sie mit der Zeit gehen oder unerschrocken nach neuen Wegen suchen – vorwärts gehen. Templa Kunststofftechnik ist nicht nur vorbildlich in puncto Flexibilität und Energiemanagement, sondern auch ein echter Hidden Champion im deutschen Mittelstand. Mit einem hohen Automatisierungsgrad, bemerkenswerter Effizienz, flachen Hierarchien und einem attraktiven Arbeitsumfeld verkörpert das Unternehmen den Idealtypus eines modernen, florierenden Unternehmens
Der Führungsstil von Peter Müller spiegelt seine langfristige Sichtweise wider. Er weiß um den Wert der Flexibilität auf dem heutigen Markt und sorgt dafür, dass Templa sich an veränderte Umstände anpassen kann, ohne Kompromisse bei Qualität und Service einzugehen.
Templa produziert für eine Vielzahl von Branchen, allerdings mit einem leichten Schwerpunkt in der Spielzeug- und Automobilbranche. Die von Haitian International Deutschland gelieferten Maschinen spielen dabei eine entscheidende Rolle, da sie ein breites Anwendungsspektrum ermöglichen und durch ihre maschinenseitige Flexibilität in der Lage sind, den Kundenanforderungen auch dann noch gerecht zu werden, wenn sich die Marktsituation – krisenbedingt oder nicht – wieder einmal ändern sollte.
Bei all dem ist Nachhaltigkeit nicht nur eine unternehmerische Anforderung an den Eigentümer und Familienvater, sondern auch eine persönliche Aufgabe. Da er auf dem Lande lebt und arbeitet, weiß er nur zu gut um den Wert der Natur und möchte seinen Teil dazu beitragen, dass auch künftige Generationen die Schönheit und den Reichtum der Natur erleben können.