In the heart of Austria, the Beneder Kompetenzgruppe is a trailblazer in plastics processing. Founded in 1965, the company has grown from modest beginnings in a garage workshop to become a versatile business known for its unique service portfolio, expertise and innovative approach.
Combining toolmaking and plastics engineering, the Beneder Group employs 45 people and delivers end-to-end solutions to customers worldwide, particularly in Europe. Characterized by family values, Beneder has steadily grown over three generations, with consistent investment in technology, talent and infrastructure. Its unique selling point? Everything from a single source: from the idea to toolmaking to the production of plastic parts and finishing techniques such as aluminum evaporation and assembly. This “one-stop solution” capability makes Beneder a particularly reliable partner and has enabled it to build long-term relationships with customers in industries such as automotive and lighting technology.
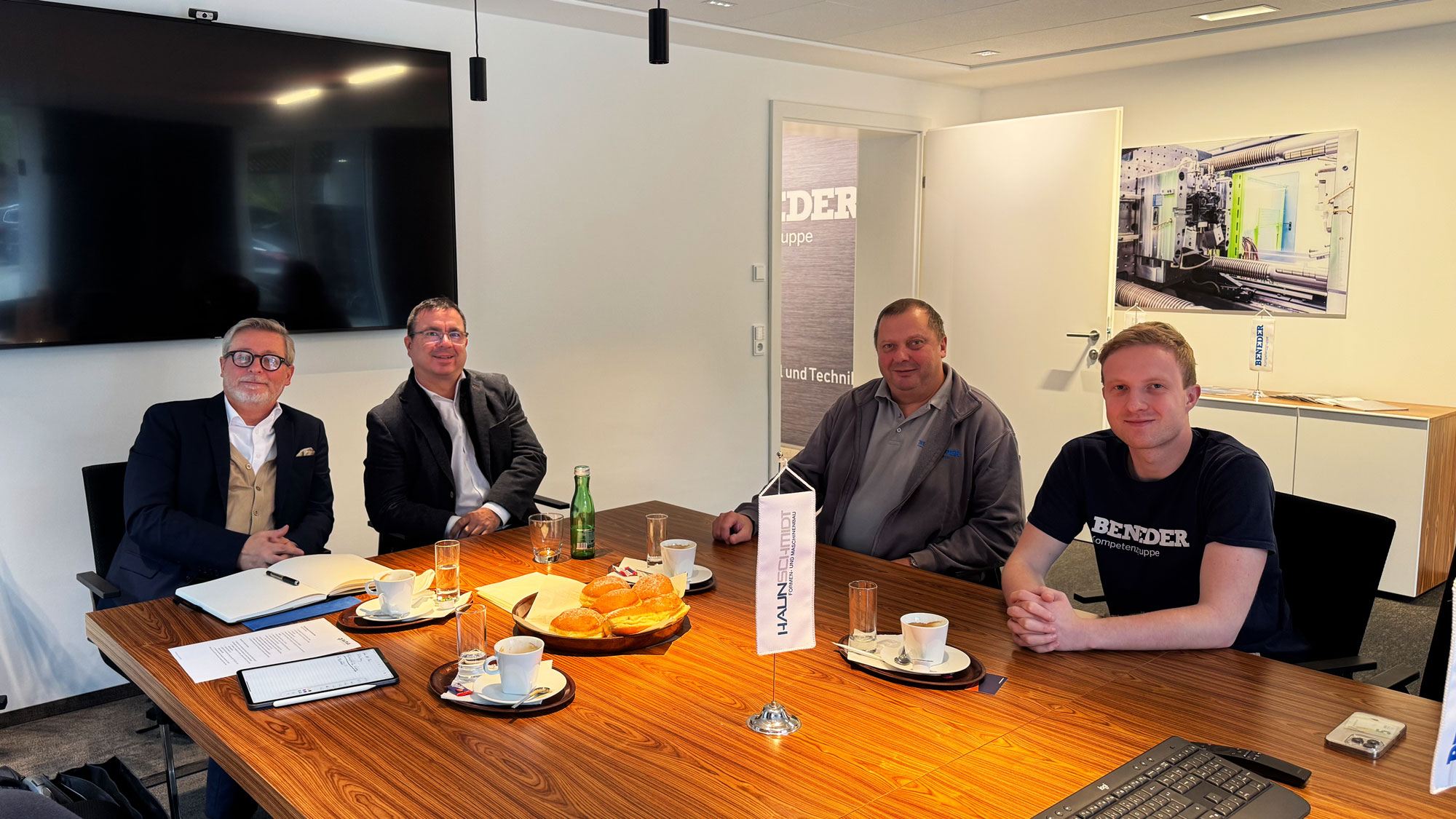
From left: Thomas Fasching (COO Büchler), Martin Büchler (Managing Director Büchler), Rudolf Derntl (Operations Manager Beneder), Lukas Beneder (Managing Director Beneder)
A day at Beneder: A look behind the scenes
We are guests in the picturesque Josefstal, accompanied by Büchler GesmbH, which has been responsible for the sales area in Austria for over 30 years and has already mastered a number of challenges together with Beneder. We are speaking with Lukas Beneder, third-generation managing director, and Rudolf Derntl, who has shaped the company for over three decades as operations manager.
As we enjoy doughnuts and coffee – it is the beginning of carneval season – Lukas Beneder and Rudolf Derntl tell us enthusiastically about their customers, the special requirements of their products and the refinements of lighting technology. Whether small series for private individuals or well-known department stores, their passion for their work is evident in every word they speak. Rudolf Derntl gives us the keys of lighting technology. 100% product quality, especially on the surfaces of reflectors and lenses, as well as the high durability of the parts, are top priorities. A large proportion of the products are also supplied to the automotive industry, where Beneder supplies components for headlights and technical parts.
But things are changing in Josefstal as well. “We are fortunate that we are less affected than others as a contract injection molder with our broad portfolio,” says Lukas Beneder. “Nevertheless, we have to operate more cleverly than before. Complexity is increasing not only on the product side, but to the same extent in business management.” Which brings us to the second important aspect besides quality: flexibility at maximum efficiency.
These circumstances led to Beneder’s first encounter with Haitian’s Zhafir electric brand last year. “Without Büchler as a local partner, we probably would not have looked into Haitian if it were not for the advantages and solid specifications of the electric Zeres,” explains Rudolf Derntl.
Lukas Beneder reports that the decision in favor of Haitian was ultimately based on a variety of factors. These included technical specifications, reliability, energy savings and, last but not least, Büchler’s expertise in selecting the appropriate peripherals, service and free on-site training. “And because the price of the machines was ‘quite ok’, we immediately added a second one,” smiles Rudolf Derntl.
A tour of the production plant
After the interesting conversation, we set off with the two of them to the production halls. The tour first takes us through the showroom, where Beneder impressively presents its extensive expertise. Production then takes place on two floors. Toolmaking on the second floor and injection molding on the second. The machinery comprises a total of 16 state-of-the-art injection molding machines.
On entering the production area, we immediately notice the numerous tools on the high shelves – flexibility and quality are indispensable for each individual machine from Beneder.
Among the machinery, we quickly spot the two Zeres machines from Haitian International, equipped with Haitian Hilectro robots. The IMM’s have a clamping force of 120 t and 60 t. “As a typical production schedule, we use the two machines to manufacture technical components and light reflectors. The average time that the tools remain on the machines is about 80 hours.” These are the only two electric machines in production to date.
At the Zeres 1200-430, Rudolf Derntl shows us the current series: a technical headlight component made of PP with 30% glass fiber. The cycle time is 15.8 seconds with two cavities. In the immediate neighborhood, the smaller Zeres 60t produces reflectors that are a prime example of precision and consistency.
“Sometimes you have to adapt a little if you usually produce on tie-bar-less machines, but otherwise we are very satisfied with the two machines,” says plant manager Rudolf Derntl. Also, the often dreaded problems with relearning a different control system were not an issue due to the intuitive menu navigation.
During our tour, we also come across a 600-ton machine (Beneder mainly produces on smaller clamping force sizes), which is no longer in regular use. “Smaller parts and series are now the trend in the industry,” explains Lukas Beneder. “The flexibility of our machinery and, of course, our many years of expertise allow us to react dynamically to these developments while ensuring the highest quality.”
A glimpse into the future
The visit at Beneder is encouraging even in difficult times. The meaningful transformation from tradition to innovation is in good hands with Lukas Beneder and his experienced team, also in the third generation. There is no shortage of skilled workers or a general lack of company know-how. Beneder has hardly any employee turnover; to date, every second apprentice has spent their entire career in the company. Although there are of course challenges that are difficult to overcome, according to Beneder, with its in-depth know-how, broad portfolio and not least the integration of modern technologies with a strong focus on quality and customer satisfaction, the Beneder Group is well prepared for the future.
We hope to continue to support the company and thank them for the pleasant visit!