https://www.templa-kunststofftechnik.com/
With the courage to change and the determination to overcome resistance, the ambitious production company Templa Kunststofftechnik has digitally interconnected its manufacturing and realigned its strategic positioning. Central momentum: energy-saving electric machines, proactive energy management, tools for greater sustainability and efficiency. And the willingness to trust in one’s common sense.
Founded in 2017, the company in Veitsaurach in central Franconia became successful as a supplier for a major toy brand. Then Corona came along, threw the order situation into disarray and caused the company to turn to being a contract molder – like so many others in the pandemic. Instead of busting their head in the sand, the team around Managing Director Peter Müller proved that even a medium-sized company can achieve a lot with a high degree of flexibility, a wealth of ideas and the courage to develop further.
Today, Templa Kunststofftechnik GmbH & Co. KG covers a wide range of competences, from product development to downstream assembly and packaging of the produced parts.
The machinery includes, among others, 22 plastic injection molding machines with clamping forces from 30 to 230 tons and shot weights from 0.1 to 500 grams, including six electric Zhafir Zeres type machines with clamping forces from 90 to 230 tons.
A wide range of materials is processed, such as thermoplastics with high filler contents (glass fiber/beads, talc), thermally sensitive plastics or high-temperature plastics (PPS, PPO, PEEK, etc.).
In total, Templa manufactures around 65 million plastic parts a year with just 12 employees on a production area of around 1,000 square meters, including hybrid components such as inserts, bushings, cores, etc. It quickly becomes clear that the team relies on lean, process-reliable production in plastics processing, right through to direct packaging of the produced parts in the delivery packaging. The entire peripherals of the injection molding machines are digitally networked, and zero-defect production has long been standard.
“Topics such as Company 4.0, Industry 4.0 or Production Strategy 4.0 are no jargon or trendy terms for us,” says Peter Müller. “They are part of our daily work and the basis of the company’s success. With our fully networked, automated and optimized processes, we can realize extremely short throughput times in injection molding and act quickly and flexibly, resulting in a very good price-performance ratio.”
The energy consumption of each individual machine is monitored and optimized using the Sensorfact energy management tool. This makes it easy to determine the power consumption of each machine and improve overall operating efficiency. It turns out that Zhafir machines have excellent consumption values in terms of energy, making them the “first choice” in production planning from now on. This arouses our curiosity; we want to know exactly and ask Peter Müller for a concrete comparison of consumption data.
In the comparison, the electric machine shows clear advantages
The setting is quickly defined: A technical part is to be produced from PP TV20 in a 28-second cycle, with a shot weight of approx. 90 g and a high demand for dimensional accuracy and quality. In competition are a hydraulic machine from a well-known manufacturer with 80 tons (green line) and a Zhafir Zeres with 120 tons (blue line), both equipped with hydraulic core pull and 6-fold hot runner control. Both machines run with a temperature control unit, which consumes about 1.5 KW which is also measured.
The result is more than clear: the Zeres performs a good third more energy-efficient.
The screenshots of the power management make it clear: The power consumption of the Zeres (blue) is about 30% lower than that of the hydraulic brand machine, which underlines the clear advantage of Haitian International’s energy-saving technology.
Peter Müller knew it all along: “When it comes to saving power, we switch on the Zeres’ first, which saves us real money.”
When asked about his expectations for the future development of the market and costs, Peter Müller smiles in a relaxed manner; he believes that his company is already in a fairly good position. “We are very efficient in the project, with a fast time to market. We have a high level of technical expertise in manufacturing, produce on energy-efficient machines, and our CO2 footprint, it’s already pretty small.”
Müller trusts the path it has taken, continuing to focus on openness to new things and innovative solutions. This has paid off in the long term, he says, citing a few examples:
- With a 3D scanner from GOM Metrology (part of the ZEISS Group), Templa and its tool suppliers have been able to “significantly reduce” their process lead times. Full-surface geometry capture through 3D scanning forms the data basis for inspecting molds and plastic parts in quality control, he said.
- The average correction loop of injection molds could be reduced by a whopping 50% to an average of 1.25 loops per mold using the CADMOULD and Varimos simulation software. “A significant time and cost savings for our customers,” notes Müller.
- In addition, he says, northern German Cleantower systems are now being used for optimized maintenance of the machines and tools. Creeping rust and lime deposits in the cooling channels “are thus a thing of the past,” and one always has “full cooling capacity and thus constant part quality.”
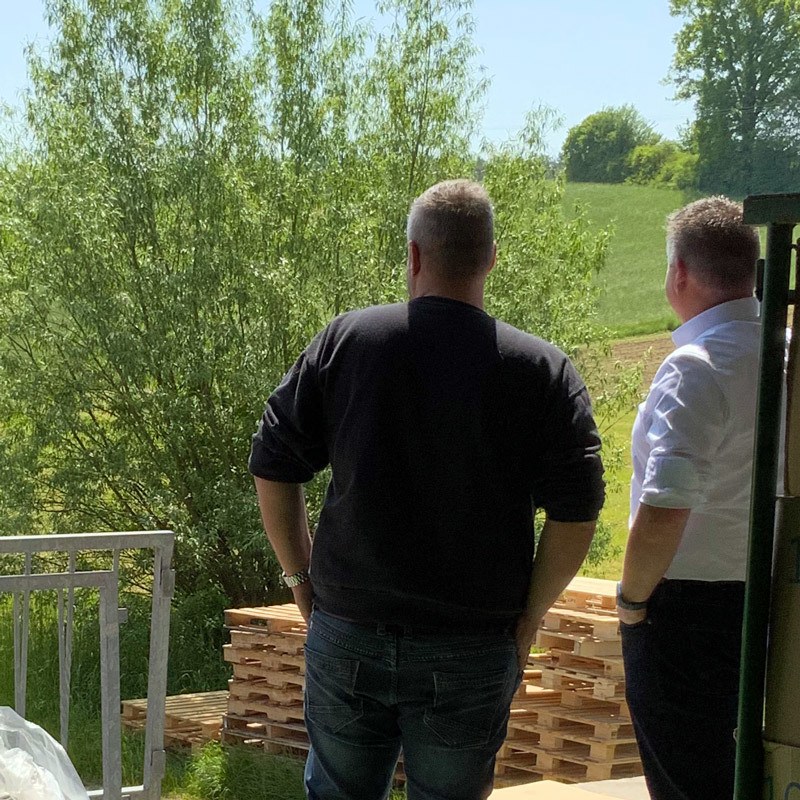
Peter Müller, Managing Director of Templa (left) and Christian Färber, Sales Partner of Haitian International Germany, take a look in the future.
A Hidden Champion with a clear mission
Templa’s success shows that even small companies can achieve remarkable results when they use advanced technologies while focusing on sustainability. When they move with the times or are undaunted in their search for new ways – forging ahead. Templa Kunststofftechnik is not only exemplary in terms of flexibility and energy management, but also a true hidden champion in the German SME sector. With a high degree of automation, remarkable efficiency, flat hierarchies and an attractive working environment, the company embodies the ideal type of a modern, thriving company
Peter Müller’s management style reflects his long-term view. He understands the value of flexibility in today’s market and ensures that Templa can adapt to changing circumstances without compromising quality and service.
Templa produces for a variety of industries, although with a slight emphasis on the toy and automotive sectors. The machines supplied by Haitian International Germany play crucial roles in this, as they enable a wide range of applications and their flexibility on the machine side enables the company to continue to meet customer requirements even if the market situation should change once again; crisis-driven or not.
In all of this, sustainability is not only a corporate requirement for the owner and family man, but also a personal mission. Living and working in the countryside, he knows all too well the value of nature and wants to do his part to ensure that all future generations can also experience the beauty and richness of nature.