“Attractive price, low consumption, smooth integration” – meeting the challenges of the times with the courage to change.
Plastium GmbH in Lauterbach, Black Forest, has established itself in the plastics processing industry over more than 50 years. The medium-sized company impressively demonstrates how to survive in a challenging market environment through a careful management with innovative technology, courage and responsibility.
The arrival of Frank Heinzelmann and Siegfried Eichinger on the management board marked a turning point in the company’s history. Back in 2020, in the middle of the coronavirus crisis, they expanded the service portfolio by acquiring additional processing companies, thus forming an efficient cluster.
Today, around 70 employees work in 3-shift operation and realize a wide range of products and services at two locations, in Lauterbach and Schiltach, from parts development with the customer to toolmaking, injection molding, assembly and logistics.
Plastium’s machine park is particularly noteworthy. The various mergers and acquisitions have resulted in a diversified machine park with around 100 machines. The clamping forces of the injection molding machines range from 20 to 350 tons, with several 2K machines also available. Overall, Plastium has machines from many different manufacturers in its ranks, now including electric machines from Zhafir.
​
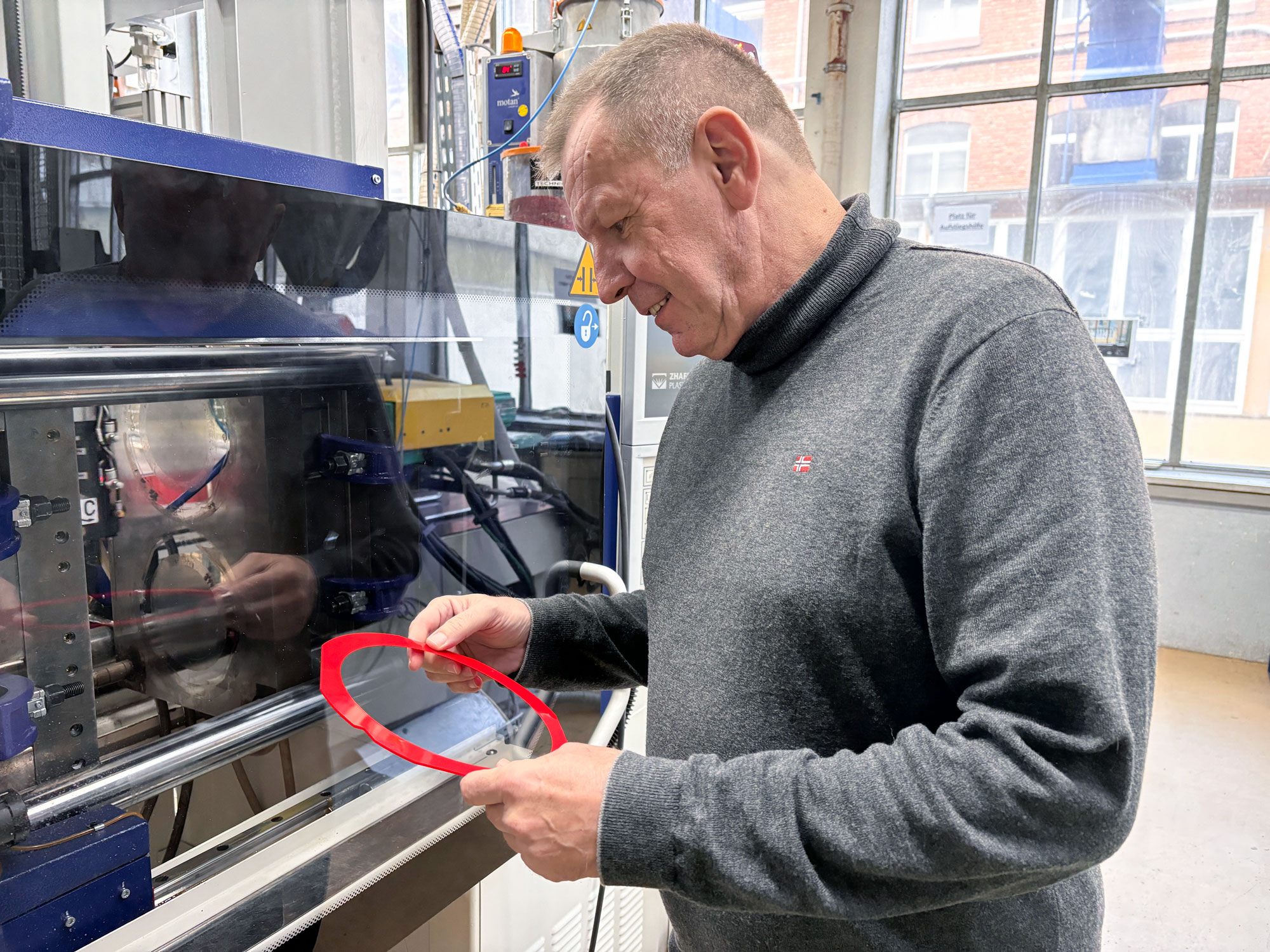
Mr. Eichinger shows a wafer frame made of SAN Tyril 790 with a shot weight of 57.2 g and a cycle time of 33 seconds sprayed on an energy-efficient Zeres 90 tons.
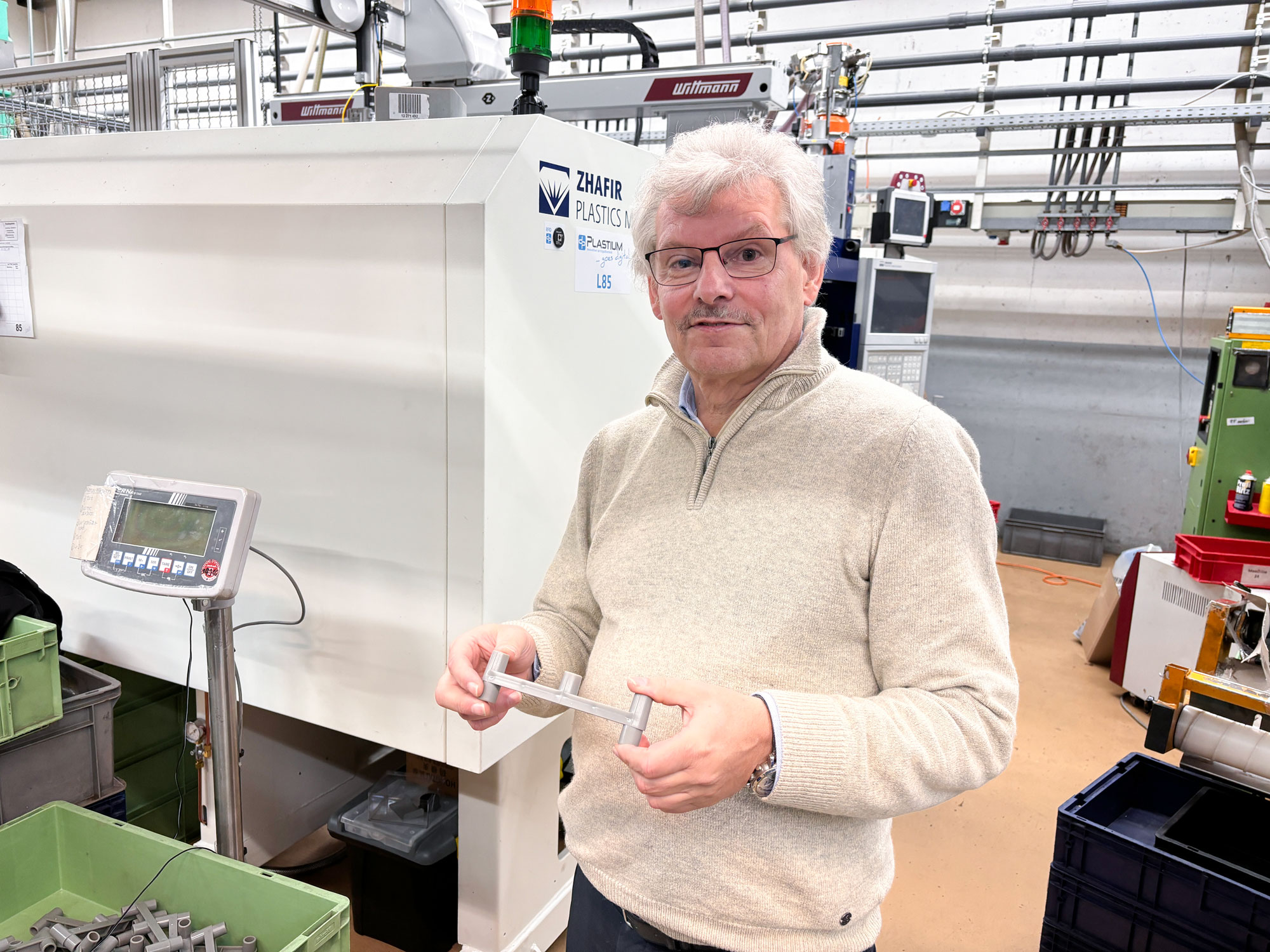
Mr. Heinzelmann shows a spacer made of Sysplast ABS regranulate, with a shot weight of 113.46 g and a cycle time of 44 seconds, injection-molded on an energy-efficient Zeres 120 tons.
Zhafir machines easily integrated into the MES
In 2023, Plastium acquired five machines from the Zhafir Zeres series, with clamping forces of 60, 90 and 120 tons. Thanks to their open connectivity and excellent energy efficiency, they are Plastium’s first choice, especially in times of rising energy and operating costs. Heinzelmann explains: “The Zeres machines are the first to be switched on and the last to be switched off in order to save energy. We installed them in May 2023 and they have been running smoothly ever since, making a significant contribution to energy efficiency.”
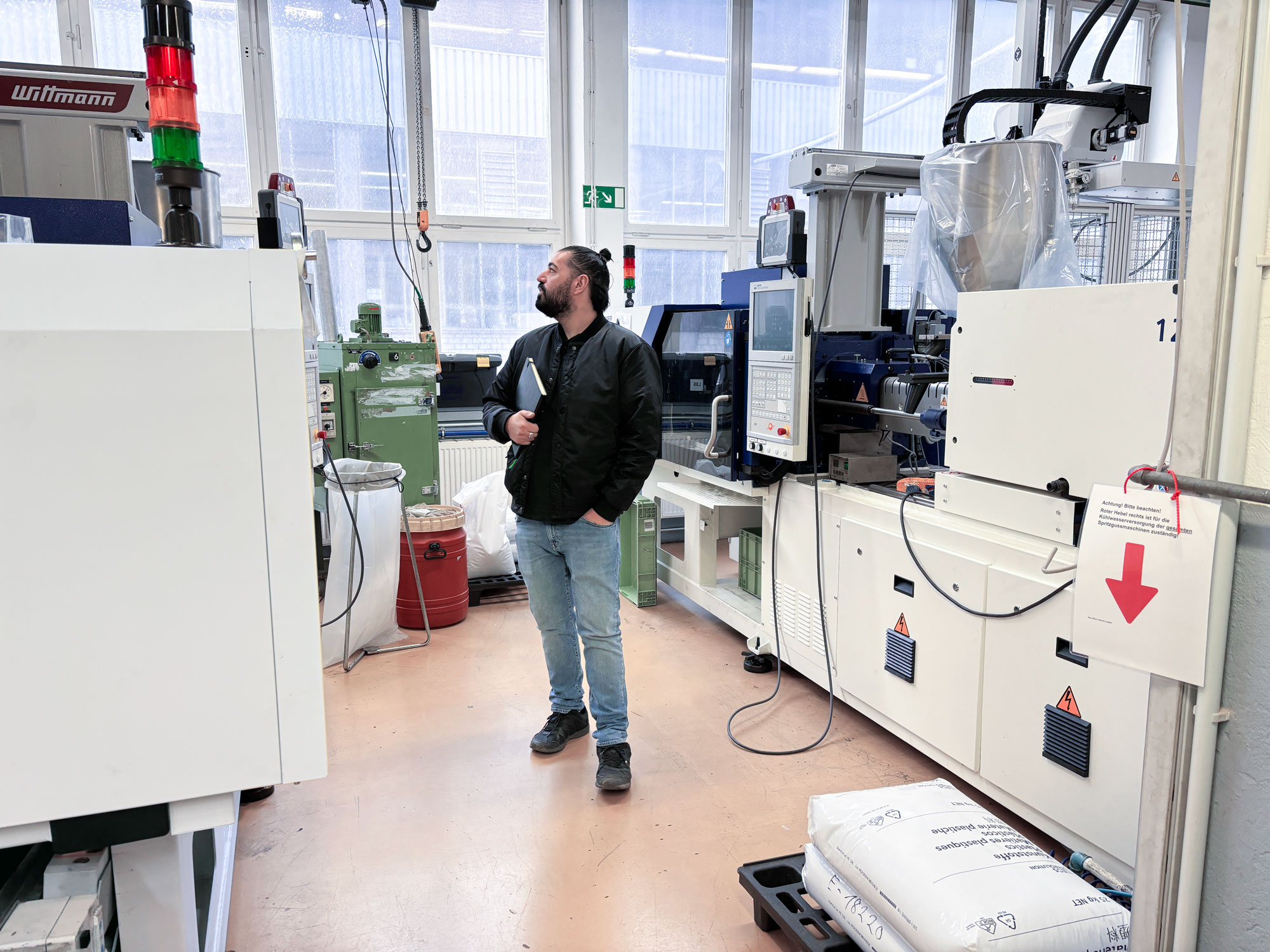
Murat Kaplan looks around to see if his “children” are all running.
Excellent service from HEWACO and HTIG
According to Heinzelmann and Eichinger, the decision in favor of Zeres was based on several factors: “The attractive price, the eligibility as an electric machine, the extremely low consumption, and the smooth integration into our MES system Pro-Ses.” In addition, the sales and service teams from Haitian International Germany and HEWACO – sales partners in south-west Germany – “made it very easy” for them, with fast response times and efficient support during integration into the MES system.
Plastium GmbH is a typical contract injection molder, but also has a broad range of in-house products in the packaging sector. The company is involved early on in the process with advice and design and has its own toolmaking department, which primarily serves to maintain and service the tools. The available application processes include 2K injection molding, assembly injection molding, insert molding and unscrewing techniques.
Plastium supplies a wide range of industries such as sanitary, electrical engineering, medical technology, automotive, etc. Plastium also produces its own products for a wide range of applications, such as universal packaging tins, boxes and trays for branded goods.
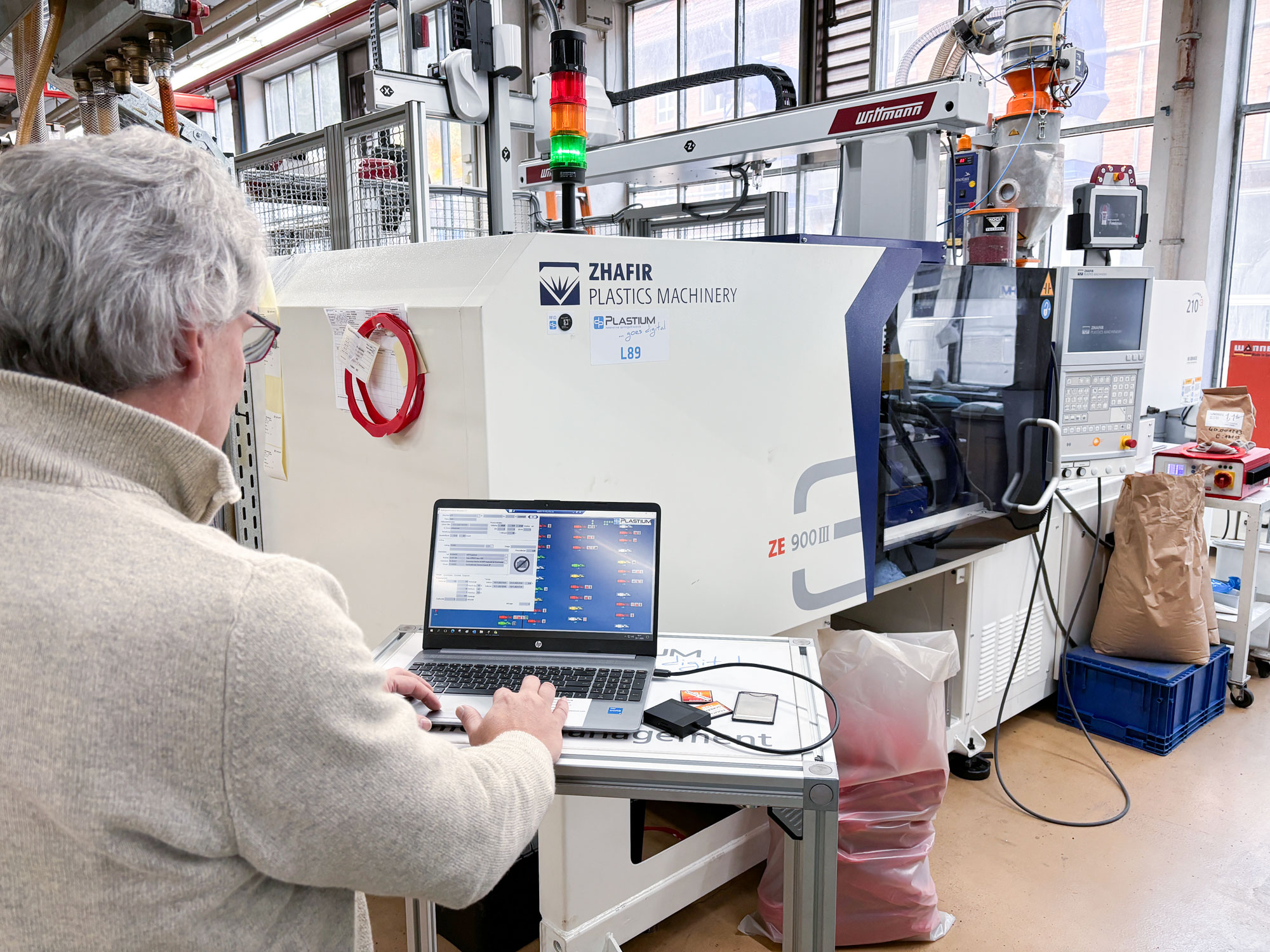
At Plastium, every machine is monitored using modern energy consumption measurements, among other things.
Energy costs reduced by more than 40 percent
The company has made remarkable progress in energy efficiency, particularly through the use of Zeres machines. “In total, these measures have led to energy cost savings of over 40 percent,” says Eichinger.
Heinzelmann and Eichinger describe the current economic situation as “challenging”, partly due to the economic slump in the second half of 2023 and the loss of purchasing power. Nevertheless, they plan to purchase further energy-saving models from Zhafir, even if they are currently waiting to see how the market develops.
Prudent corporate management with a view to the future
Plastium is using various strategic levers to emerge stronger from the current economic situation. These include reducing costs, particularly energy costs, generating new volumes through online marketing strategies, investing in modern QM equipment, and expanding in the direction of Industry 4.0. The managing directors attach great importance to process monitoring and energy consumption measurements to stand out from the competition in terms of technology.
In addition to saving energy, the fair and social treatment of employees is a major issue at Plastium. Here, the company is seen as an organism in which every part is important and attempts to meet the needs of the employees. For example, by investing in technology, training and health management, but also through flexible arrangements in terms of place of work and working hours.
In terms of sustainability, the management believes that the company is not only well positioned in terms of energy, but also aims to have a positive impact on the region. As the largest employer in Lauterbach, the company believes it has a responsibility to survive in the long term and contribute to the regional economy.
With a clear, confident view of the future and a philosophy that goes beyond pure profit, Plastium appears well equipped to continue to be an important player in the plastics industry in the future.
Latest News from Plastium:
Big even when it’s small
Shortly before the end of the year, Plastium welcomed 3 siblings (7, 9, 10 years old) who built a miniature injection molding machine from many plastic building blocks at home.
The new “big” machine has also been successfully in use at Plastium since June 2023 and produces high-precision plastic components in an energy-efficient manner.
The proud “builders” with their mother and Plastium employee were welcomed by the managing directors Frank Heinzelmann and Siegfried Eichinger and were allowed to see the big brother of their model in action in production.
After all the excitement and the new impressions in an unfamiliar environment, the children were delighted to receive an Eruopa Park voucher as a small thank-you.
“Plastium’s work with young talent can’t start early enough”!
In terms of sustainability, the management believes that the company is not only well positioned in terms of energy, but also aims to have a positive impact on the region. As the largest employer in Lauterbach, the company believes it has a responsibility to survive in the long term and contribute to the regional economy.
With a clear, confident view of the future and a philosophy that goes beyond pure profit, Plastium appears well equipped to continue to be an important player in the plastics industry in the future.
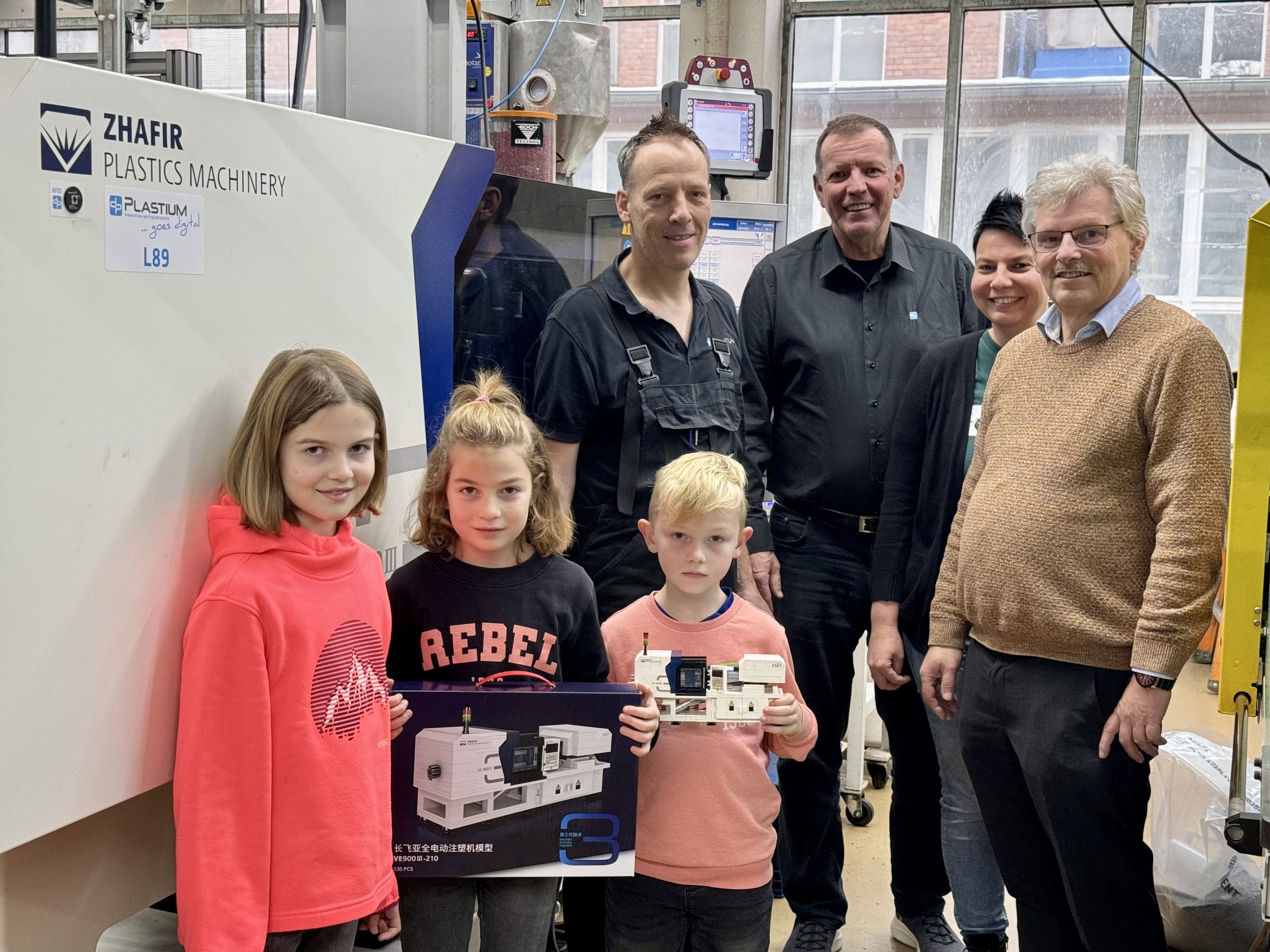
The siblings and proud “builders” of the miniature injection molding machine with (from left to right) Production Manager Martin Lauble, Siegfried Eichinger, Manuela Fehrenbacher and Frank Heinzelmann.